EMI shielding tapes play an important role in safeguarding electronic devices from electromagnetic interference (EMI). With the increasing dependence on technology in our everyday lives, EMI has become a major concern for both manufacturers and consumers. EMI can lead to interference, interrupt signal transmission, and even damage sensitive electronic components. This comprehensive guide explore everything you need to know about EMI shielding tapes – from their importance, functionality, and types to their application and benefits. Whether you are a manufacturer looking to protect your products or a consumer seeking to understand the importance of EMI shielding tape, this post will provide you with the in-depth knowledge you need.
Understanding EMI Shielding Tapes
As mentioned earlier, shielding tapes serve the purpose of safeguarding sensitive electronic components against electromagnetic interference, thereby enhancing their overall functionality. These EMI shielding tapes consist of a conductive backing material, commonly copper or aluminum, which is combined with a pressure-sensitive adhesive for easy application onto various surfaces. The conductive backing serves as a protective barrier by either obstructing or redirecting electromagnetic waves, effectively preventing any form of disruption to electronic devices.
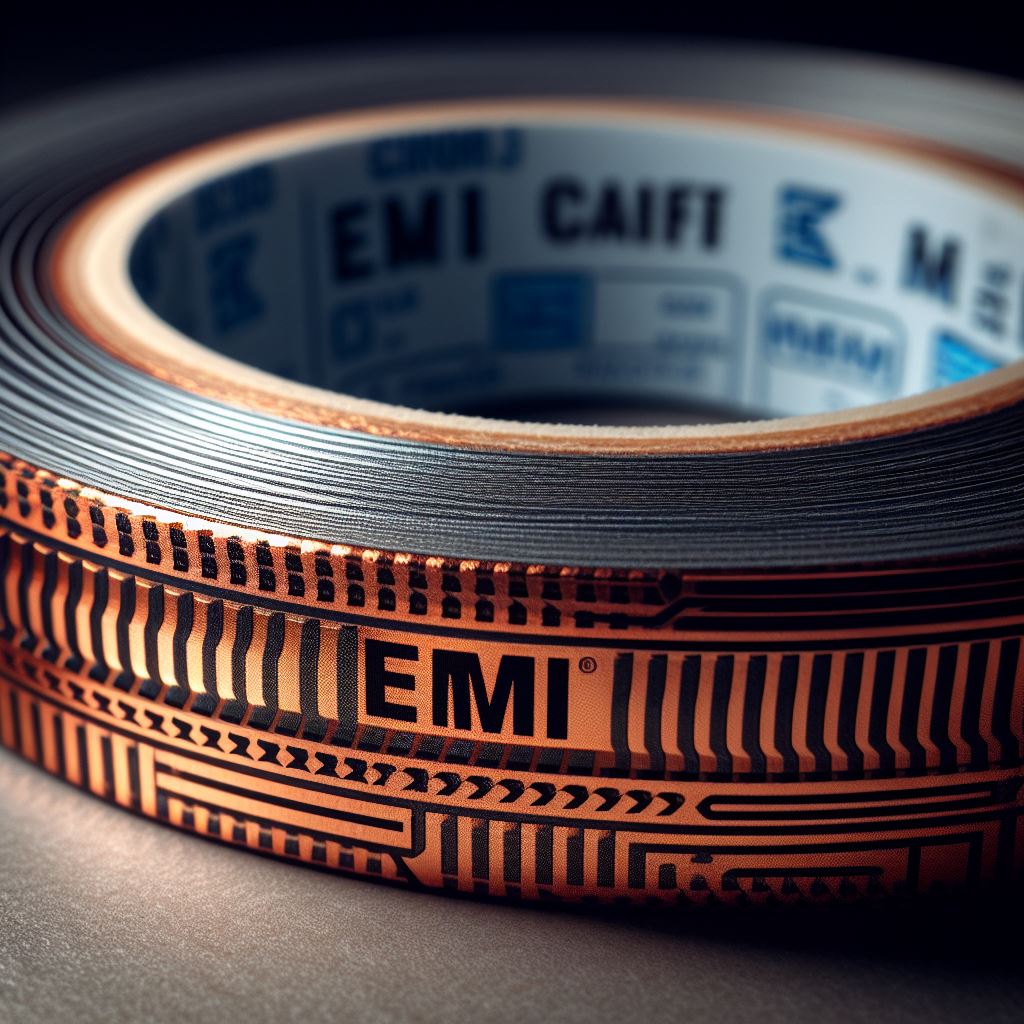
Importance of EMI Shielding Tapes
The following key reasons add to the popularity of EMI shielding tapes
- Regulatory Compliance: In various industries, including aerospace, medical, and military sectors, there are stringent regulations in place pertaining to electromagnetic compatibility (EMC) and EMI shielding. To adhere to these regulations and ensure the reliability of their products in diverse environments, businesses largely depend on EMI shielding tapes. By employing such tapes, companies can ensure that their products meet necessary standards and maintain optimal performance.
- Signal Integrity: It is of utmost importance to ensure the integrity of signals in high frequency electronics. However, the presence of EMI can largely disrupt the transmission of signals within a circuit, leading to signal distortion or weakening. Shielding tapes serve as an effective solution by providing a conductive pathway that redirects and dissipates unwanted electromagnetic waves. Thus, these tapes help preserve the integrity of signals and minimize the potential for data corruption.
- Component Longevity: Electronic components, especially those with sensitive microchips and circuits, are highly vulnerable to EMI damage. The use of shielding tapes, creates a protective layer, effectively shielding the components from the harmful effects of electromagnetic radiation. Employing shielding tapes significantly reduces the potential for premature failure, whilst also adding to the overall lifespan of devices.
- Design Flexibility: EMI shielding tapes offer a flexible and practical design solution that seamlessly integrates into various applications. Available in adhesive tape and foil formats, these tapes enable the creation of customized solutions to meet specific requirements. With their versatility, EMI shielding tapes have become a favored choice across several industries looking for reliable protection against electromagnetic interference.
- Cost-Effective Solution: EMI shielding tapes are a cost-effective solution compared to many other EMI shielding methods, such as conductive coatings. These tapes can be easily applied to specific areas, minimizing material costs, while also reducing the need for challenging or time-consuming redesigns or modifications in existing designs.
Working Mechanism of EMI Shielding Tapes
The below-given steps would help you understand the working mechanism of EMI shielding tapes.
- When an electronic device is exposed to electromagnetic waves, the conductive material within the tape serves as a reflective barrier, thus blocking most of the electromagnetic energy from entering the protected area. The conductivity of the material used in the tape plays a large role in reflecting and repelling incoming electromagnetic waves.
- The conductive particles in the shielding tape are designed in a way to convert the electromagnetic energy into heat, dissipating it throughout the material. This absorption process further reduces the amount of electromagnetic energy that can affect the overall functioning of electronic devices.
- Lastly, the adhesive backing on the EMI shielding tape enables secure attachment of the tape to the surface of the electronic device or enclosure. This guarantees uninterrupted shielding coverage and prevents any gaps that could allow electromagnetic waves to enter the tape.
It is important to note that the effectiveness of the tapes can vary depending on several factors, including, tape thickness, material composition, and areas of application. Therefore, it is highly advisable to choose the appropriate tape based on the specific requirements of the electronic device or system.
Installation of EMI Shielding Tapes
There are several steps involved in the proper installation of EMI shielding tapes. The steps must be properly carried out to ensure proper functionality and effectiveness.
- Prepare the Surface: Ensure that the area of application is thoroughly cleaned and dried before applying EMI shielding tape. You can use a mild solvent or alcohol-based cleaner to proceed with the cleaning process.
- Measure and Cut: Carefully measure the length of the area where the shielding tape will be applied. Now make a clean cut using sharp, clean scissors or a knife and cut the tape to the appropriate length.
- Peel Off the Liner: Carefully remove the liner from one end of the tape, without coming in contact with the adhesive side. Ensure to peel off the liner smoothly, avoiding any folds or wrinkles in the tape.
- Apply the Tape: Apply the tape evenly on the surface, starting from one end and slowly progressing towards the other. You can use a clean, lint-free cloth to firmly press the tape onto the surface, guaranteeing optimal contact with the substrate and proper adhesion. If there is any excess tape, trim it using a scissor, making neat, clean cuts.
- Inspect and Test: Following the installation process, carefully examine the tape for the presence of air bubbles, wrinkles, or loose edges. If there are any imperfections found, utilize a squeegee or your finger to correct them. Furthermore, test the effectiveness of the EMI shielding by using appropriate testing equipment.
Types of EMI Shielding Tapes
There are several types of EMI shielding tapes available on the market, each with its unique properties and applications. A few of them include:
- Copper Foil Tapes: These tapes are highly conductive and have excellent adhesive properties, making them largely chosen for applications where conductivity and adhesion are crucial. They find immense applications across electronic devices, printed circuit boards, and electrical grounding, among others.
- Aluminum Foil Tapes: These tapes and known to offer high shielding effectiveness and have the ability to block radio frequencies effectively. They find applications in aerospace, telecommunications, and medical devices, radio frequency interference (RFI) is a concern.
- Conductive Fabric Tapes: Made from conductive fabric material, these tapes are widely known for their flexibility and conformability. They are largely chosen for applications that require EMI shielding in curved or irregular surfaces.
- Conductive Foam Tapes: Made from soft and flexible material infused with conductive particles, these foams create an electrically conductive path, providing effective shields against electromagnetic interference. These tapes are commonly used in applications where flexibility and conformability are of utmost importance, such as the electronics industry.
- Flame-Retardant EMI Shielding Tapes: Made from special materials that have been treated with flame-retardant additives, these tapes not only provide protection against electromagnetic interference but also resist wide temperature range. They are largely chosen in the automotive and construction industries.
How to Select the Right EMI Shielding Tape
How to choose the most appropriate shielding tap from so many different options available on the market? Here are a few factors to consider when choosing the right tape for your specific needs.
- Shielding Effectiveness: Ensure to invest in tapes that have been certified and tested to meet industry standards including the Military Standard MIL-STD-285 or ASTM D4935. These certifications ensure that the tapes provide the required level of shielding for your specific application as they have undergone rigorous testing throughout their manufacturing stage.
- Material Composition: The material composition of the tape determines its performance. Common materials used in EMI shielding tapes include copper, aluminum, or a combination of both. Copper is known to offer excellent electrical conductivity, while aluminum provides lightweight and cost-effective shielding. Consider the specific requirements of your application, such as conductivity, weight, and cost, to determine the most suitable material composition.
- Compatibility: Different tapes are available in the marketplace that are designed for specific applications and substrates. Before choosing a tape, consider the substrate you will be bonding it to, along with considering specific environmental conditions it will be exposed to. Ensure that the EMI shielding tape is compatible with the chosen substrate.
- Adhesive Type: When selecting tapes for applications, it is crucial to prioritize those with conductive adhesives. These offer a strong bond and low resistance, guaranteeing a reliable connection between the tape and the surface. By maximizing the effectiveness of the shielding, conductive adhesives contribute significantly to overall performance. Additionally, consider the application method for the tape and choose a pressure-sensitive adhesive if ease of use is important.
- Temperature and Environmental Resistance: When selecting EMI shielding tapes, it is crucial to consider their resistance to different environmental conditions, such as extreme temperatures and moisture. It is advisable to choose tapes that are resistant to these factors to ensure long-term performance. Invest on tapes that are rated for the temperature range and environmental conditions in which they will be used.
Application Areas of EMI Shielding Tapes
EMI shielding tapes find immense applications across various industries. A few of them are listed below.
- Electronics and Telecommunications: The tapes are beneficial in protecting circuit boards, connectors, cables, and other electronic components from the harmful effects of EMI.
- Aerospace and Defense: These tapes are used in radar systems, communication equipment, guidance systems, avionics, and military vehicles.
- Medical Devices: They are used to protect sensitive medical equipment such as MRI machines, monitoring devices, pacemakers, and other electronic medical devices.
- Industrial and Manufacturing: They are found useful in safeguarding sensitive equipment from EMI generated by machinery, power lines, control panels, data acquisition systems, and other electrical devices.
- Renewable Energy: The tapes are used in solar panels, inverters, wind turbines, and energy storage systems.
- Automotive and Transportation: These tapes are applied to wiring harnesses, connectors, sensors, displays, and other electronic components.
How to Maintain the Performance of EMI Shielding Tapes
Being one of the essential components of many electronic devices and systems, EMI shielding tapes must be maintained and inspected at regular intervals of time. It is advisable to follow the below-listed maintenance tips if you are using the tapes.
- Regular Visual Inspection: Perform a visual inspection of the tapes regularly to check for any signs of damage or wear. The tape should be immediately replaced in case of any tears, cracks, or peeling edges are found.
- Cleanliness: Cleaning the surface of the tape using a soft, lint-free cloth and a mild detergent helps to remove dirt, oils, or other contaminants. Do not use harsh chemicals or abrasive materials for cleaning purposes. as they can damage the tape.
- Reapplication: The adhesive properties of the tapes may weaken, leading to performance issues. It is advisable to remove and reapply the tapes periodically to guarantee their optimum adhesion and performance.
- Temperature and Humidity: EMI shielding tapes can be sensitive to extreme temperatures and humidity levels. Hence, in order to ensure optimal performance, it is crucial to store these tapes in an environment that falls within the specified temperature and humidity range. Exposing the tapes to excessive heat or moisture may result in a loss of their effectiveness.
- Manufacturer's Guidelines: Always follow the manufacturer's guidelines and recommendations for the specific type of EMI shielding tape you are using. Each tape may have specific storing and maintenance procedures that should be followed to guarantee the expected level of performance.
Now that you know all the must-know things about EMI shielding tapes; it is also necessary to be aware of some of their downsides, such as limited shielding effectiveness, application precision, durability concerns, high costs associated with certain materials, thermal concerns, weight, limited flexibility, poor compatibility with surfaces, maintenance and inspection, limited reusability, and so on. If you require a high level of EMI shielding effectiveness and have the resources to design and manufacture custom shielding solutions, board level shields may be the better option. This is where board level shields can make a difference. This post ends by letting you know about a leading EMI shielding solutions provider, XGR Technologies. The company provides revolutionary, multi-cavity shields SnapShot® EMI shields. These board level shields can be thermoformed to virtually any shape. The shields have a non-conductive, polyetherimide inner surface and conductive, tin plated outer surface resulting in exceptional shielding performance in an ultra-lightweight and low profile solution. Contact the team at XGR Technologies and see what best they can offer to achieve the highest level of EMI protection.