SnapShot® Board Level EMI Shield
The electronic devices are getting smaller by the day, and as a result, PCB designs are getting increasingly miniature and complex. Furthermore, with the demand for wireless devices increasing, electromagnetic and radio frequency interference (EMI/RFI) is becoming a concern for PCB designers. This EMI/RFI may affect everything from components to PCBs. The integration of board level shielding is crucial to protect components and PCBs from EMI, ensuring optimal performance and regulatory compliance. By mitigating EMI, board level shields advance electronic sophistication in our interconnected world.
XGR Technologies SnapShot EMI shields are revolutionary, multi-cavity shields that solve many of the problems and challenges associated with today’s board level shielding (BLS) technologies. Originally developed by W.L.Gore & Associates, XGR Technologies has acquired all assets related to the SnapShot® board level EMI shielding business. These board level shields were launched in 2002 and have been successfully used in military radios, drones, avionics, GPS devices, industrial handheld scanners, medical imaging equipment, and network computing for over 20 years.
SnapShot® board level EMI shields consist of a lightweight, metallized plastic material that is thermoformed into virtually any design. The shields have a non-conductive, polyetherimide inner surface and conductive, tin plated outer surface resulting in exceptional shielding performance in an ultra-lightweight and low profile solution.
Why Use SnapShot® EMI Shield?
Superior Shielding Effectiveness
SnapShot® board level shields provide superior shielding effectiveness when compared to traditional frame and lid style EMI shields. The traditional board level EMI shields can consume excess board real estate and make it difficult or impossible to inspect the board components after reflow. Traditional shields are also very difficult to remove and replace if rework is necessary. These board level shields are made in two-piece designs, provide lower shielding effectiveness, and add significantly more weight. When compared with the traditional EMI cover and frame for PCB, the SnapShot® board level shield is a one-piece board level shield (BLS) that is attached to the PCB after reflow utilizing small solder spheres mounted to the board. SnapShot® board level shielding is installed on PCB by snapping the oval holes in the shield around the perimeter of the cavity over the solder spheres. These solder spheres are attached to PCB during the reflow in the exact same manner as a standard component.
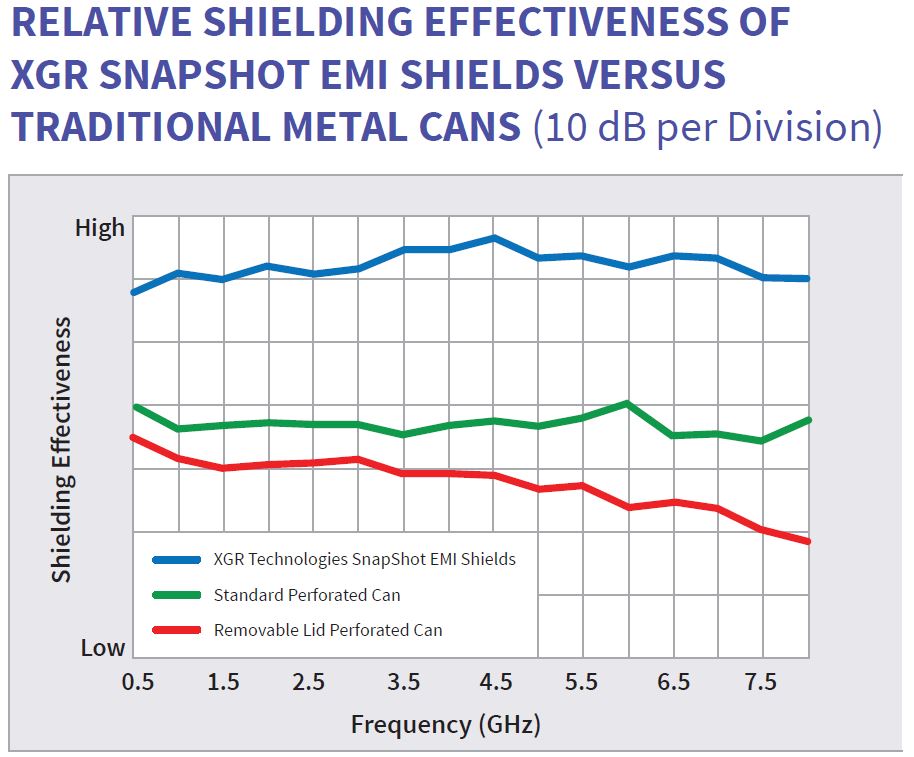
SnapShot® board level EMI shields outperform other competitive options with shielding effectiveness from below 1 GHz up to 18 GHz. The shield offers extremely consistent isolation across a wide frequency range. SnapShot® board level shields feature a non-conductive interior surface, which helps reduce electromagnetic coupling with circuit traces, eliminates shorting threats, and minimizes the overall volume and weight.
Extremely Rugged and Durable
- The SnapShot® board level EMI shield is proven rugged and durable in extreme conditions.
- The DC resistance across each solder sphere to shield connection has been extensively tested, meeting stringent XGR Technologies requirements across the following methods and standards:
- Mechanical Shock (JEDEC JESD 22-B104-B)
- Bump (IEC 60068-2-29)
- Vibration (IEC 60068-2-64)
- Thermal Shock (MIL-STD-883E Method 1010.7B)
- Accelerated Aging (85°C / 85 RH)
- SnapShot® EMI shields has been proven in the field for nearly two decades in the most demanding rugged applications, including:
- Military Handheld Radios
- Military Drones
- Military Avionics
- Military Weapons Systems
- Industrial Handheld Computers and Scanners
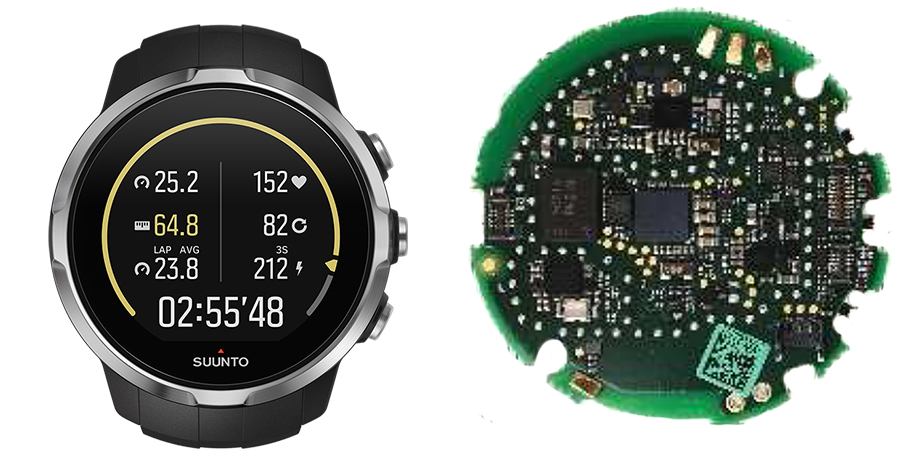
Installs After Reflow
- Solder sphere attachment mechanism enables unobstructed visual or automated optical inspection and re-work
- Note the solder sphere layout in this GPS watch PCB after reflow.
- SnapShot® EMI shield is easily installed AFTER the reflow and inspection process
Removable and Replaceable
If necessary, the board level shield is removable and replaceable multiple times without damage to the board or components; NO additional heat steps or soldering are required.
These removable board level shields are thermoformed, which allows the designers to lay out the shield enclosure to fit the circuits. The traditional board level EMI shields constrain the layout of the circuit to their rectangular shapes and can be removed only using special types of tools. These removal techniques are expensive, damaging, and warrant immediate repair. When compared to these traditional board level EMI shields, our replaceable board level shields do not constrain the circuit layout to their dimensions and can be removed whenever required.
Designed to Virtually Any Shape
- The thermoforming process in a custom mold for each application enables maximum design freedom
- SnapShot® EMI shield fits your board layout rather than you having to lay out your board to accommodate a square or rectangular boards. As a part of custom board level shielding, we can design them to suit any of the following:
- Radii/circles for round boards
- Angles
- Irregular lines
- True multi-cavity
- 3D topography
- Perforations for heat dissipation
- No perforations
- Multiple height profiles
- Low profile with zero clearance
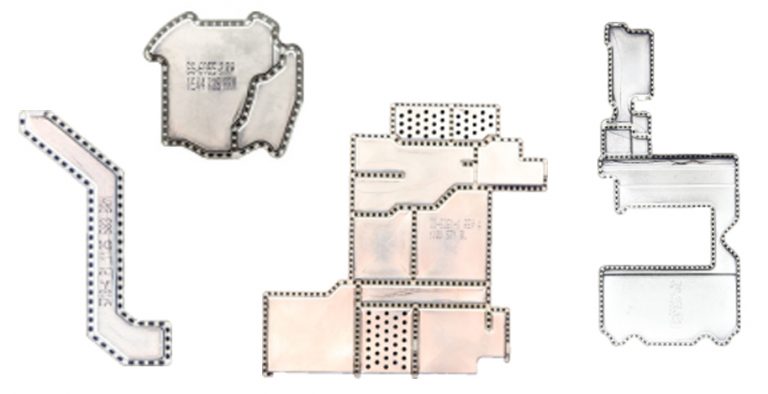
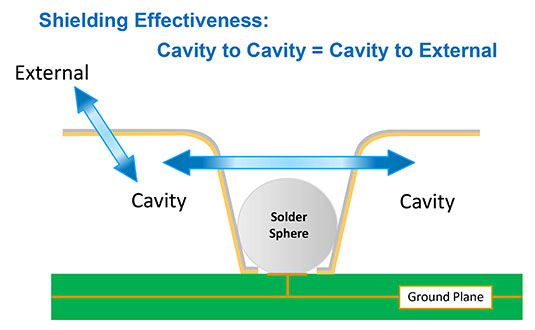
Multi-Cavity Capability
- Solder spheres attached to the ground plane enable complete isolation of adjacent cavities
- Shielding effectiveness between cavities equals the performance from cavity to external
- Multi-cavity board level shielding SnapShot® replaces 9 discrete frame and lid cans
Saves Valuable PCB Real Estate
SnapShot® board level shielding (BLS) technology can save up to 50% in trace width required between shielded cavities. The technology leads to PCB space savings.
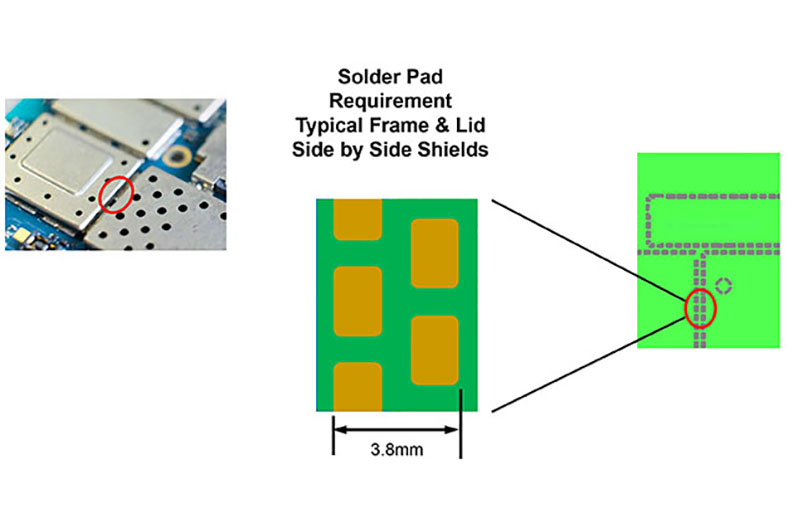
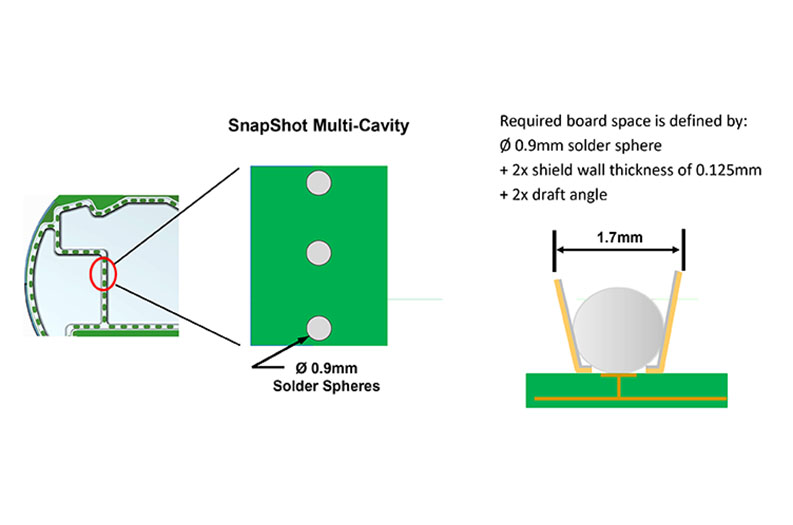

Extremely Lightweight
- SnapShot® board level EMI shields are the lightest weight board level shields available
- The unique material has 6x lower density than typical steel EMI cans
- SnapShot® board level shields are based on a thin film of polyetherimide with a density of 1.27 g/cm3. When compared to the density of cold rolled steel at 7.87 g/cm3, it is easy to see why SnapShot® shields are 80 to 90 percent lighter weight.
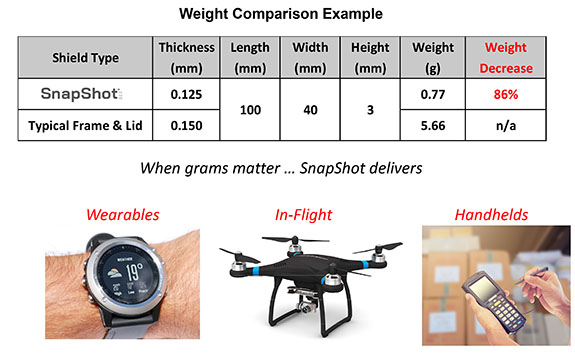
Low Profile
- SnapShot® is the LOWEST PROFILE board level shield available.
- The inner surface of the SnapShot® EMI Shield is non-conductive, polyetherimide
- SnapShot® EMI shields require NO clearance between the top of the component and the inner surface of the shield
- Designing the shield to have an interference fit with the top of the IC results in low profile and enhanced thermal dissipation.
- Our low profile board level EMI RFI shields are entirely made in the USA.
The shields are attached to the PCB via a patented attachment mechanism utilizing individual BGA solder spheres. The shield is installed when oval holes around the shielded cavity perimeter “snap” over solder spheres that have been reflowed to the ground plane.

The diameter of the solder sphere is larger than the valley between the shield walls. This durably connects (snaps) the shield to the board and ground plane.
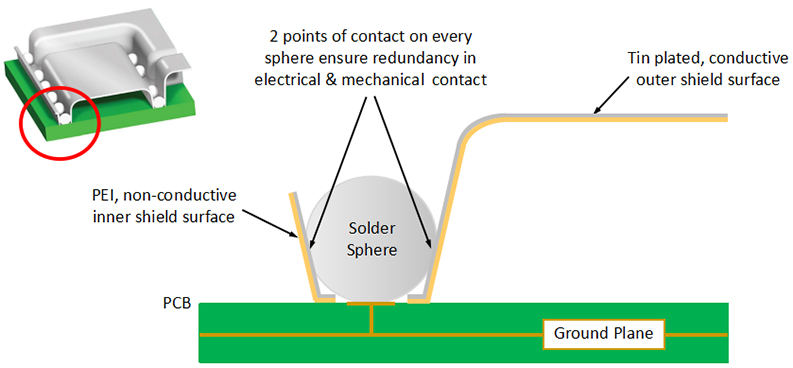
After the solder spheres are permanently soldered to the ground plane during reflow, the shield is aligned with an installation tool and pressed down into place.
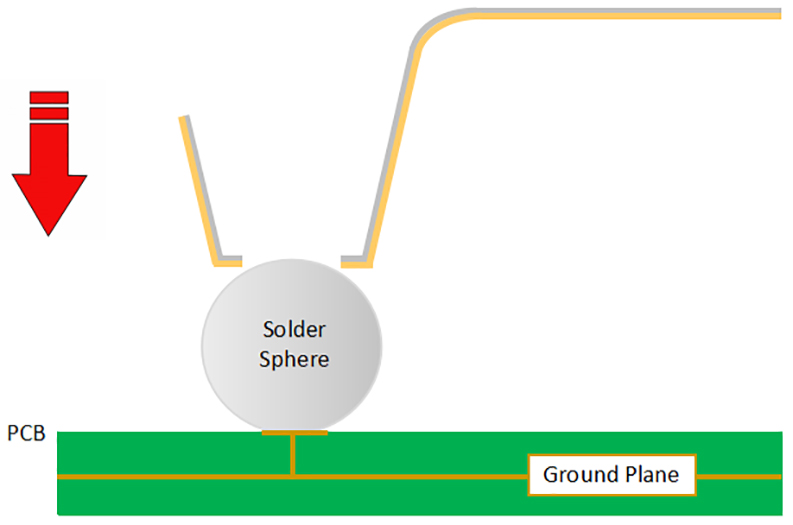
The shield flexes as the holes around the cavity perimeter are forced over the solder spheres with the use of an installation tool.

Once the shield passes the midpoint of the sphere, the natural forces pull the shield down to the board and exert continuous force to keep the shield in place.
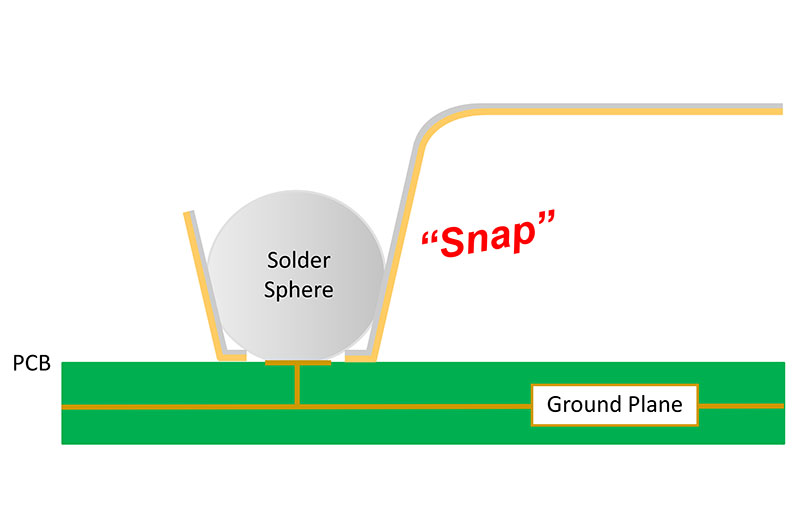
Installation Tooling
An installation tool with “teeth” is used to press the shield over the solder spheres and onto the board. The individual teeth press the shield between solder spheres to ensure a secure attachment at each sphere.
Installation tools are machined aluminum which are designed and manufactured by XGR Technologies.
Various methods of alignment, such as alignment pins as shown here, can be used to ensure an accurate and precise installation every time.

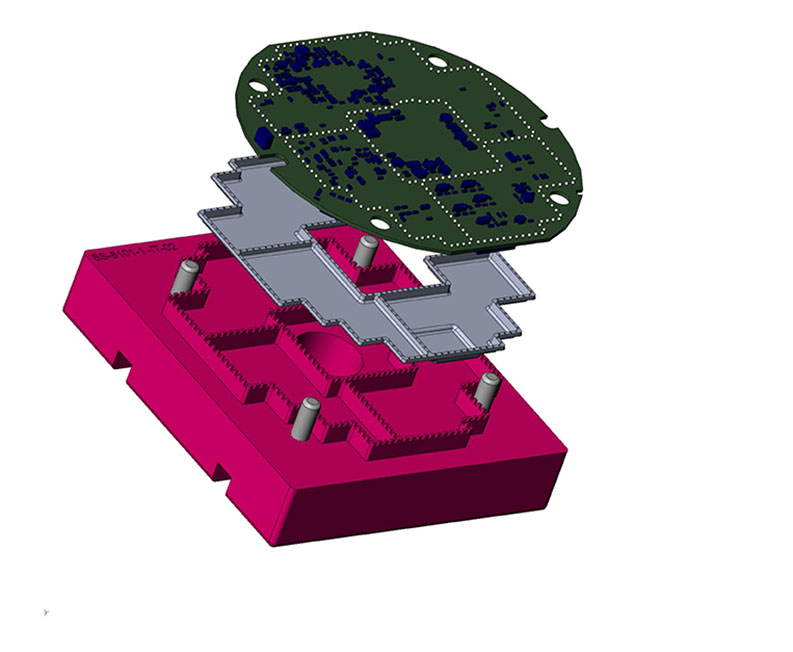
Process Flow
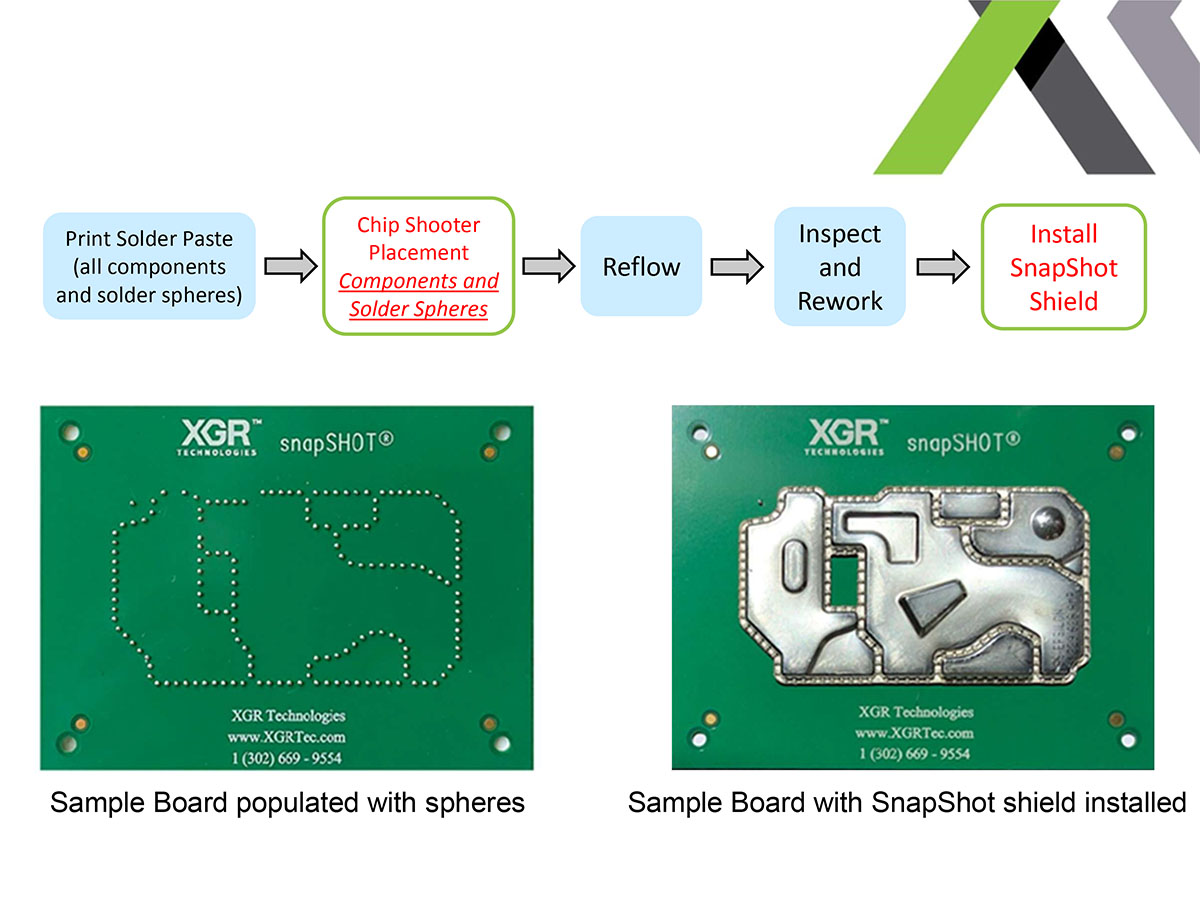
Click Below for How It's Installed Video
How SnapShot® Board Level Shield is Made
SnapShot® board level EMI shields are made by thermoforming a proprietary engineered material. The base material is polyetherimide, which is well known for it’s combination of low weight, high strength, and high temperature capability.
XGR Technologies utilizes a proprietary plating process to create a conductive, tin plated surface on one side of the material. This becomes the outer, conductive surface of the SnapShot® board level shield.
Note, the inner surface remains non-conductive allowing for minimal to zero clearance required between board components and the shield.

The process of making your custom board level shield begins with close collaboration between you and the XGR engineering team. In this collaboration, customer design files are reviewed by the XGR engineering team, ideas for optimization are discussed, and cavities to be shielded are identified.
Next, XGR will create a 3D model of the proposed EMI shield(s) along with optimal placement of solder spheres along a ground trace. Once the design is finalized including complete interference checks, the mold(s) are created and the finished parts delivered to the customer.
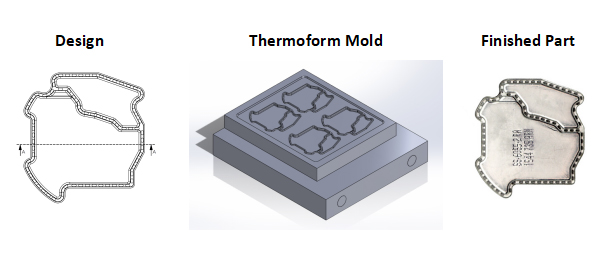